Business
Six Sigma 101: Project Management Methodology
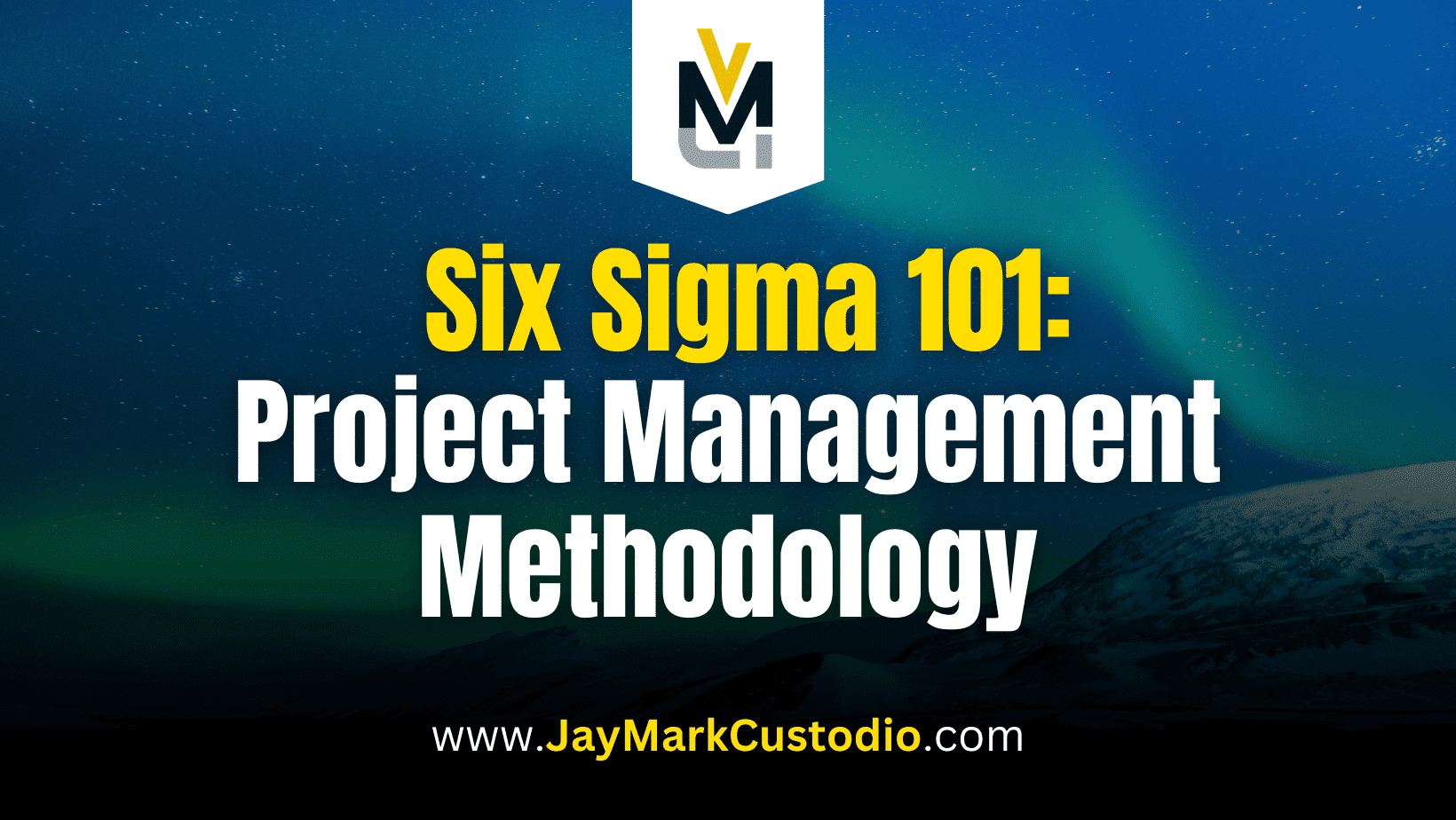
Six Sigma is a comprehensive methodology that aims to improve business processes by minimizing errors and defects, thereby increasing efficiency, productivity, and customer satisfaction.
Table of Contents
The methodology consists of five levels, each crucial in achieving process improvement.
First Level: Define the Problem or Improvement
The Define level of Six Sigma is the first and probably the most critical level in the Six Sigma methodology. At this level, businesses identify the process that needs improvement and set the project’s scope. The objective here is to understand what the customer wants and expects from the process.
In the Define level, the business must also identify the relevant stakeholders and set measurable goals. It is essential to identify the stakeholders who have a significant impact on the process. These stakeholders can be internal or external to the organization. Once the stakeholders are identified, the business must understand their expectations and requirements from the process.
Setting measurable goals is another critical aspect of the Define level. These goals should be specific, measurable, achievable, relevant, and time-bound (SMART). The goals should also align with the customer’s requirements and expectations. Once the goals are set, the business can move to the next level, which is the Measure level.
Second Level: Measure the Current performance of the process and identify areas that need improvement
The Measure level of Six Sigma is the second level in the Six Sigma methodology. At this level, the business measures the current performance of the process and identifies areas that need improvement. The objective of this level is to collect data on the process’s inputs, outputs, and performance metrics, such as cycle time, defect rate, and customer satisfaction.
To measure the process’s current performance, the business must establish a baseline for the process. This baseline represents the current state of the process and provides a reference point for future improvements. Once the baseline is established, the business can collect data on the process’s inputs, outputs, and performance metrics.
The data collected in the Measure level should be accurate, reliable, and relevant. The business can use various tools and techniques to collect data, such as surveys, questionnaires, interviews, and statistical analysis. Once the data is collected, the business can move to the next level, which is the Analyze level.
It is important to note that the Measure level is critical in identifying the root cause of the process’s problems. Without accurate and reliable data, the business may not be able to identify the root cause of the process’s problems. Therefore, the Measure level is a crucial step in the Six Sigma methodology.
Third Level: Analyze the data collected
The Analyze level of Six Sigma is the third level in the Six Sigma methodology. At this level, the business analyzes the data collected in the Measure level to identify the root cause of defects and inefficiencies. The objective of this level is to use statistical tools such as regression analysis, hypothesis testing, and process mapping to identify the causes of performance issues.
In the Analyze level, the business must examine the data collected in the Measure level to identify patterns, trends, and relationships between the process’s inputs, outputs, and performance metrics. The business must also use statistical tools to test hypotheses and determine whether the data supports the hypothesis.
Regression analysis is one of the statistical tools used in the Analyze level. It helps businesses understand the relationship between the process’s inputs and outputs. Hypothesis testing is another tool used in the Analyze level. It helps businesses test whether the data supports a particular hypothesis or not. Process mapping is also used in the Analyze level to identify the flow of the process and identify areas of improvement.
Once the root cause of the process’s problems is identified, the business can move to the next level, which is the Improve level. It is essential to note that the Analyze level is critical in identifying the root cause of the process’s problems. Without accurate and reliable data analysis, the business may not be able to identify the root cause of the process’s problems. Therefore, the Analyze level is a crucial step in the Six Sigma methodology.
Fourth Level: Improve the Process
The fourth level, “Improve,” involves developing and implementing solutions to address the root cause of the process’s problems. This level entails generating and evaluating ideas to improve the process, selecting the most appropriate solution, and implementing the solution.
The Improve level of Six Sigma is the fourth level in the Six Sigma methodology. At this level, the business develops and implements solutions to address the root cause of the process’s problems. The objective of this level is to generate and evaluate ideas to improve the process, select the most appropriate solution, and implement the solution.
In the Improve level, the business must generate a list of potential solutions to the process’s problems. These solutions should be based on the data collected and analyzed in the previous levels. Once the list of potential solutions is generated, the business must evaluate each solution to determine its feasibility, cost-effectiveness, and impact on the process.
After evaluating the potential solutions, the business must select the most appropriate solution to implement. The selected solution should be based on the data collected and analyzed in the previous levels and should address the root cause of the process’s problems.
Once the solution is selected, the business must implement the solution and monitor its effectiveness. The implementation of the solution may require process changes, employee training, or new equipment. It is essential to monitor the effectiveness of the solution and make adjustments as necessary.
The Improve level is critical in implementing solutions that address the root cause of the process’s problems. Without effective solutions, the process may continue to produce defects and inefficiencies. Therefore, the Improve level is a crucial step in the Six Sigma methodology.
Fifth Level: Control the Process
The Control level of Six Sigma is the fifth and final level in the Six Sigma methodology. At this level, the business monitors and controls the process to ensure that the improvements are sustained. The objective of this level is to develop and implement control plans to maintain the gains achieved in the previous levels.
In the Control level, the business must develop control plans to monitor the process and ensure that it continues to operate at the improved level. The control plans should include procedures for measuring performance, identifying defects, and taking corrective action. The business must also establish a system for monitoring the process and ensuring that the improvements are sustained.
It is essential to note that the Control level is critical in ensuring that the improvements made in the previous levels are sustained. Without effective control plans, the process may revert to its previous state, producing defects and inefficiencies. Therefore, the Control level is a crucial step in the Six Sigma methodology.
Businesses must follow a rigorous and structured approach to implement Six Sigma principles. This approach involves identifying the process that requires improvement, understanding the customers’ requirements, collecting data on process performance, analyzing the data to identify root causes, developing and testing solutions, and implementing control measures to ensure sustainability.
By following the Six Sigma methodology, businesses can achieve significant process improvement, enhance their overall performance, and increase customer satisfaction.